![]() | Since the end of 2018, we have started the sale and integration of the robots of the Danish MIR (Mobile Industrial Robots). These robots participate in the corporate logistics in a fully collaborative way: they are suitable for carrying pallets (MIR500), towing, transportation. The scope of application is expanded by different superstructures, such as storage racks, conveyors, robotic arms, tow hooks, lifts. |
Based on a preliminary measurement, we can offer a demo with our own demo-robot either at our facility or on-site.
Calculations show a return within a year, thus it is a great solution for compensating for labor shortage, as well as for developing an innovative factory.
Calculations show a return within a year, thus it is a great solution for compensating for labor shortage, as well as for developing an innovative factory.
![]() | MiR100 Capacity: 100 kg Towing: 300 kg | ![]() | MiR200 Capacity: 200 kg ESD | ![]() | MiR200 + Hook Towing: 500 kg ESD |
![]() | MiR250 Capacity: 250 kg ESD | ![]() | MiR500 Capacity: 500 kg ESD | ![]() | MiR1000 Capacity: 1000 kg ESD |
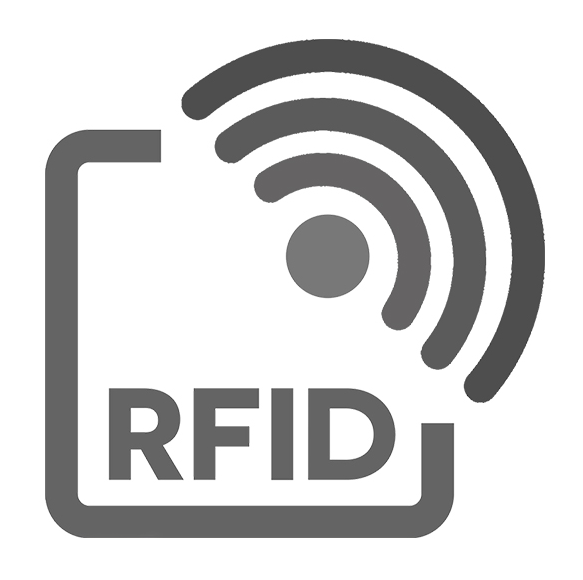
RFID (Radio Frequency IDentification), as the name suggests, is device identification technology by radio frequency. It has become widely popular for identifying and monitoring devices used in manufacturing processes. The hardware consists of two parts: a passive data medium (TAG) and an active antenna that also serves as a data processor. Each TAG has a unique ID (UID) that ensures the identification of any device it has been connected to.
Furthermore, industrial TAGs also have memory for writing and reading, thus are suitable for storing process-specific data and statuses.
![]() | RFID TAGs TAGs available in hundreds of different sizes and functions Printable label Miniature, heat-resistant, screwable Available with magnetic, metal and plastic housing Different frequency ranges (LF, HF, UH) | ![]() | RFID read/write heads, antennas Read heads for communication with the TAGs can be selected according to what tasks they would be utilized for. They are available with internal or external processors, for various industrial communication protocols (RS232, RS485, IO Link, EIP, Profinet, EtherCAT). |
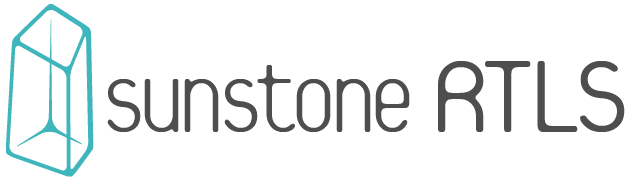
RTLS (Real-Time Location System), as the name suggests, is a system used for tracking the location of objects within a building or other enclosed area in actual time. In certain cases, it is necessary to be able to locate a device within a factory or determine where it was previously at a specific time or time range. For such tasks, RFID is not, or just partially, capable.
The hardware of RTLS also consists of two main parts. The mobile transmitter (TAG) is an active device that transmits data via radio signals at defined intervals. These signals are received by reference points (Anchors) installed at fixed locations throughout the monitored area. TAGs are capable to transmit a huge amount of useful data (such as ID, temperature, atmospheric pressure, acceleration data, etc.) in a very short time. Based on their distance from the Anchors, the position of a TAG can be estimated by triangulation method.
![]() | Potential usage of the RTLS system: Monitoring movement of products Calculating cycle time (packages/boxes, machines, conveyor belts) Machine and equipment utilization Equipment inventory, search support Measuring employee movement Ensuring necessary distance between employees Characteristics of the system: Precision: 0.3 - 0.5 m Number of devices: max.1500-2000 TAG/zone, 7 Anchor Possible size of the zone: 1500-2000 m2 More zones can cover entire factories. Custom developed user interface |
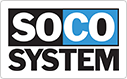
![]() | Powered and gravity conveyors are indispensable parts of the different intralogistic systems. They can be found at almost every manufacturing company where any handling task is presented. Based on utilization, there are numerous different designs, with different capacity, width and length. These conveyors often need to be integrated into the production system to achieve continuous manufacturing. Customized design is a serious engineering task, especially in case of more complex systems. To reduce production time and costs, we use the modular line elements of the Danish SOCO System for the majority of our projects. |
![]() | ![]() | ![]() | ![]() | ![]() | ![]() |
Roller conveyor, straight | Fixed curve with wheel axles | Driven conveyor with rollers, straight | Curves with conical rollers | Belt conveyor with submounted driving | Belt conveyor with booster, 2 section |